Як оформити пластикові деталі
Короткий опис:
До дизайн пластикових деталейполягає у визначенні форми, розміру та точності деталей, виходячи з ролі, яку відіграють деталі у виробі, та правила процесу лиття пластмаси. Кінцевим результатом є креслення для виготовлення форми та пластмасової частини.
Виробництво виробів починається з дизайну. Конструкція пластикових деталей безпосередньо визначає реалізацію внутрішньої структури, собівартості та функції виробу, а також визначає наступний крок виготовлення прес-форми, вартість та цикл, а також процес лиття під тиском та процес подальшої обробки та вартість.
Пластикові деталі широко використовуються в різних виробах, приміщеннях та житті людей у сучасному суспільстві. Пластикові деталі вимагають різної форми та функцій. Вони використовують пластикові матеріали, і їх властивості різноманітні. У той же час існує безліч способів виготовлення пластикових деталей у промисловості. Тож проектувати пластикові деталі - непроста робота.
Різна конструкція деталей та матеріал виробляється різною обробкою. Процес лиття пластмас в основному включає нижче:
1. лиття під тиском
2. видувне лиття
3. компресійне лиття
4.ротаційне лиття
5.термоформування
6. екструзія
7.виготовлення
8. піноутворення
Існує безліч способів їх масового виробництва. Лиття під тиском є популярним методом виготовлення, оскільки лиття під тиском 50% ~ 60% пластикових деталей виробляється за допомогою лиття під тиском, це високошвидкісна виробнича можливість.
Вітрина для деяких пластикових деталей, які ми розробили:
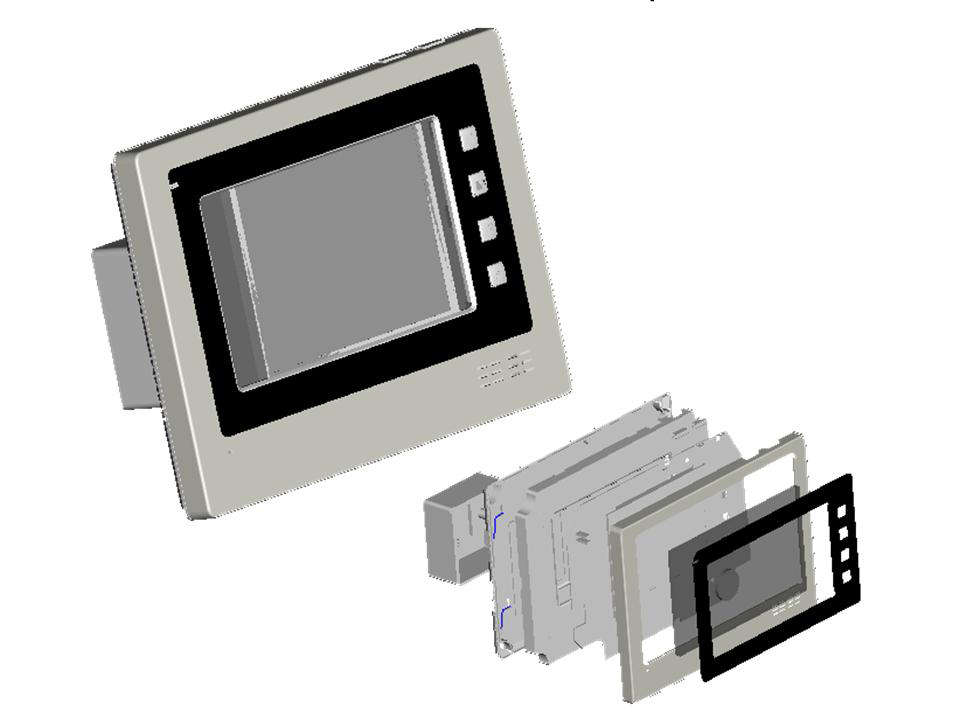
Пластиковий корпус телефону для зору
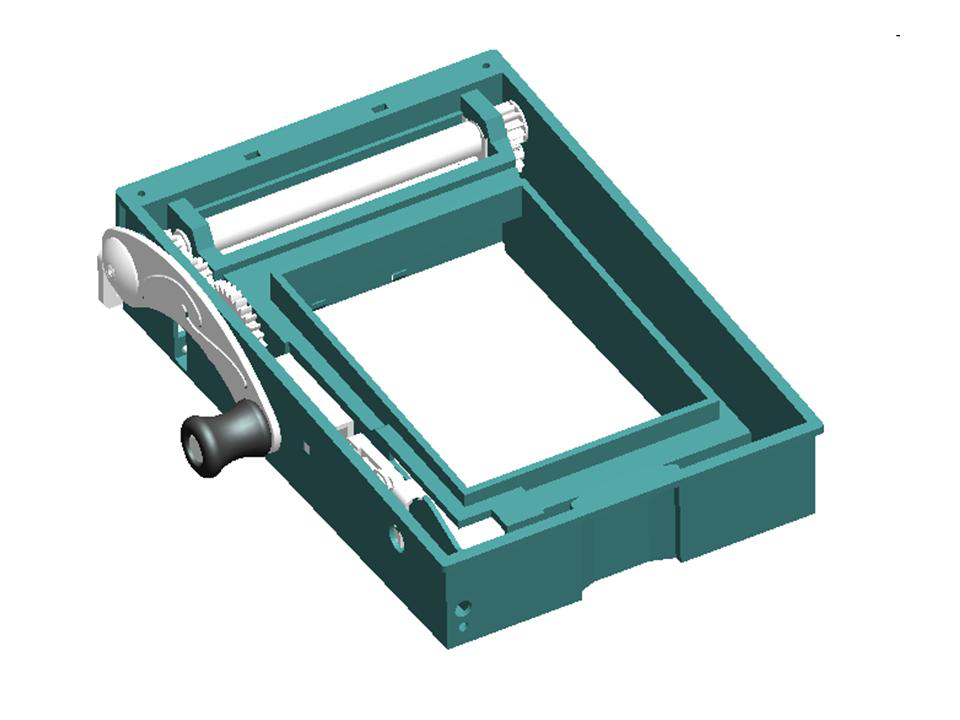
Пластикові деталі механізму
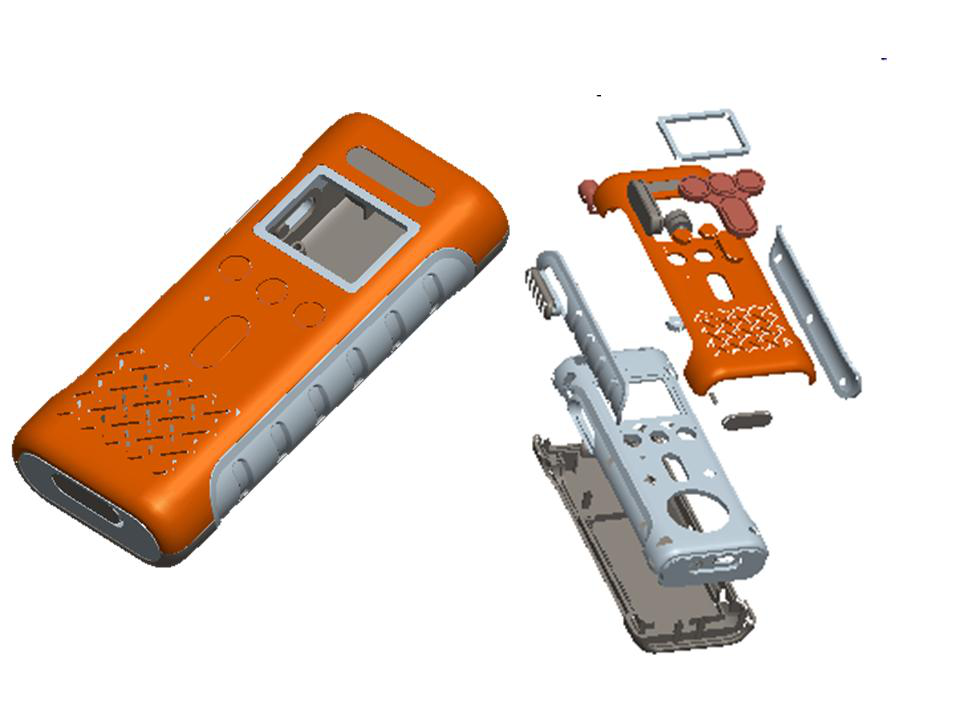
Пластикові футляри електронних
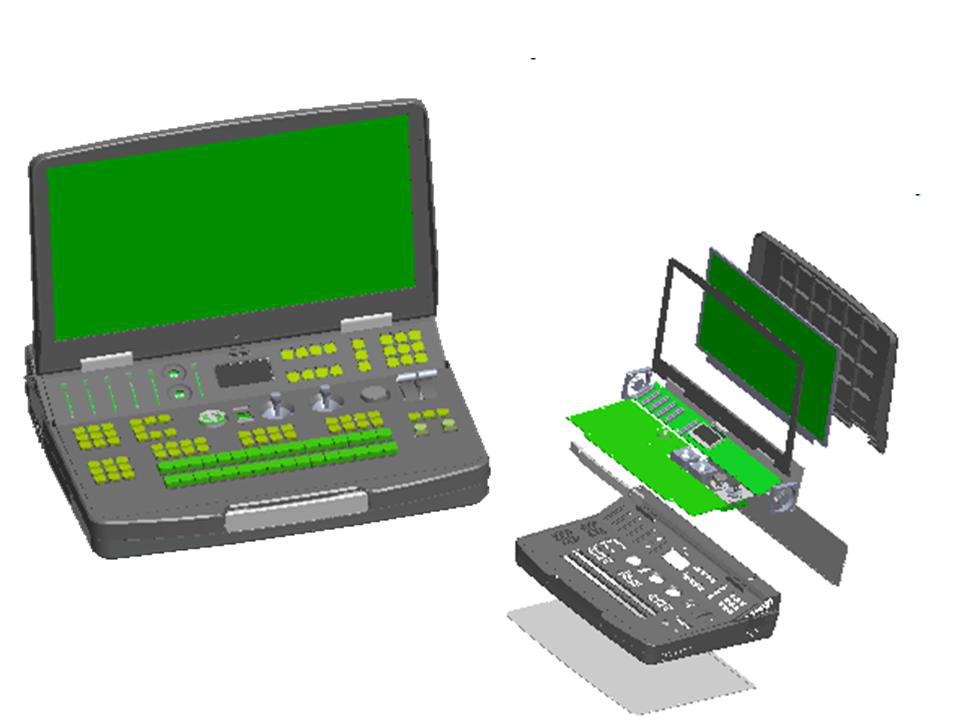
Пластиковий корпус для інструменту
Нижче ми поділимося деталями проектування пластикових деталей у трьох аспектах
* 10 порад щодо дизайну пластикових деталей, які ви повинні знати
1. Визначте зовнішній вигляд дизайну та розмір виробу.
Це перший крок у всьому процесі проектування. Відповідно до маркетингових досліджень та вимог замовника визначають зовнішній вигляд та функції продуктів та формулюють завдання з розробки продуктів.
Відповідно до завдання на розробку, команда розробників проводить аналіз технічної та технологічної доцільності продукту та створює 3D-модель зовнішнього вигляду товару. Потім, згідно з реалізацією функції та складанням продукту, плануються можливі деталі.
2.Відокремте окремі деталі з креслень виробу, виберіть тип пластикової смоли для пластикових деталей
Цей крок полягає у відокремленні деталей від 3D-моделі, отриманої на попередньому кроці, та оформленні їх як індивідуальних. Відповідно до функціональних вимог деталей вибирайте підходящу пластикову сировину або металовироби. Наприклад, АБС зазвичай використовується в
оболонка, ABS / BC або ПК повинні мати певні механічні властивості, прозорі деталі, такі як абажур, стійка лампи ПММА або ПК, деталі шестерні або зношені деталі POM або нейлон.
Після вибору матеріалу деталей можна починати дизайн деталей.
3. Визначте кути тяги
Кути тяги дозволяють видалити пластик з форми. Без кутів тяги деталь мала б значний опір через тертя під час зняття. Кути тяги повинні бути присутніми з внутрішньої та зовнішньої сторони деталі. Чим глибша деталь, тим більший кут тяги. Просте емпіричне правило - мати кут тяги 1 градус на дюйм. Відсутність достатнього кута тяги може призвести до подряпин по боках деталі та / або великих позначок штифтів ежектора (про це далі).
Кути тяги зовнішньої поверхні: Чим глибша деталь, тим більший кут тяги. Просте емпіричне правило - мати кут тяги 1 градус на дюйм. Відсутність достатнього кута тяги може призвести до подряпин по боках деталі та / або великих позначок штифтів ежектора (про це далі).
Зазвичай для того, щоб мати гарний вигляд поверхні, текстуру роблять на поверхні деталей. Стіна з фактурою шорстка, тертя велике, і вивести її з порожнини непросто, тому потрібен більший кут нанесення. Чим грубіша текстура, тим більший кут складання потрібен.
4. Визначте товщину стінки / рівномірну товщину
Формування твердої форми не бажане при литті під тиском з наступних причин:
1) .Час охолодження пропорційний квадрату товщини стінки. Тривалий час охолодження твердих речовин переможе економіку масового виробництва. (поганий провідник тепла)
2). Більш товста секція зменшується більше, ніж більш тонка, тим самим вводячи диференціальну усадку, що призводить до деформації або сліду раковини тощо (характеристики усадки пластмас та характеристики pvT)
Тому у нас є основне правило для дизайну пластикових деталей; наскільки це можливо, товщина стінки повинна бути рівномірною або постійною назовні деталі. Ця товщина стінки називається номінальною товщиною стінки.
Якщо в деталі є суцільний переріз, його слід зробити порожнім, ввівши серцевину. Це повинно забезпечити рівномірну товщину стінки навколо серцевини.
3). Які міркування при вирішенні товщини стінки?
Він повинен бути досить товстим і жорстким для роботи. Товщина стінки може становити від 0,5 до 5 мм.
Він також повинен бути досить тонким, щоб швидше охолоджуватися, що призведе до меншої ваги і вищої продуктивності.
Будь-які зміни товщини стінки повинні бути мінімальними.
Пластикова деталь із різною товщиною стінки зазнає різної швидкості охолодження та різної усадки. У такому випадку досягнення близької толерантності стає дуже важким і багато разів неможливим. Там, де різниця товщини стінки є важливою, перехід між ними повинен бути поступовим.
5.Конструкція з'єднання між деталями
Зазвичай нам потрібно з'єднати дві оболонки разом. Для утворення закритого приміщення між ними розмістити внутрішні компоненти (блок друкованої плати або механізм).
Звичайні типи підключення:
1). Закріплювальні гачки:
З'єднання за допомогою гачок зазвичай використовується у виробах малого та середнього розміру. Його характеристика полягає в тому, що гачки, як правило, встановлюються по краю деталей, і розмір виробу може бути зменшений. У зібраному стані він закривається безпосередньо без використання інструментів, таких як викрутка, ультразвукова зварювальна плашка та інші. Недоліком є те, що засувки можуть спричинити ускладнення цвілі. Повзунковий механізм і механізм підйому необхідні для реалізації з'єднання затискних гачків і збільшення вартості прес-форми.
2). Гвинтові з'єднання:
Гвинтові з'єднання є міцними та надійними. Зокрема, кріплення гвинт + гайка є дуже надійним і довговічним, що дозволяє проводити багаторазове розбирання без тріщин. Гвинтове з'єднання підходить для виробів з великою силою замикання та багаторазового демонтажу. Недоліком є те, що гвинтова колона займає більше місця.
3). Монтажні боси:
З'єднання кріплення заглиблень полягає у фіксації двох деталей шляхом щільної координації між виступами та отворами. Цей спосіб з'єднання недостатньо міцний, щоб дозволити розбирати вироби. Недоліком є те, що міцність фіксації зменшиться із збільшенням часу розбирання.
4). Ультразвукове зварювання:
Ультразвукове зварювання полягає у введенні двох деталей в ультразвукову форму та сплавленні контактної поверхні під дією ультразвукового зварювального апарату. Розмір виробу може бути меншим, ін'єкційна форма порівняно проста, а з'єднання міцним. Недоліком є використання ультразвукової форми та апарату для ультразвукового зварювання, розмір виробу не може бути занадто великим. Після демонтажу ультразвукові деталі не можна використовувати знову.
6. Підрізання
Підрізання - це предмети, які заважають видаленню будь-якої половини форми. Підрізання можуть з’являтися де завгодно в дизайні. Це настільки ж неприйнятно, якщо не гірше, ніж відсутність кута тяги на деталі. Однак деякі зниження є необхідними та / або неминучими. У таких випадках це необхідно
підрізи виробляються шляхом ковзання / рухомих деталей у формі.
Майте на увазі, що створення підрізів дорожче при виробництві прес-форми і повинно бути мінімальним.
7. Підтримка ребер / ластовиці
Ребра в пластиковій частині покращують жорсткість (залежність між навантаженням і деформацією деталі) деталі та підвищують жорсткість. Це також підвищує здатність до цвілі, оскільки вони прискорюють потік розплаву у напрямку до ребра.
Ребра розміщені вздовж напрямку максимального напруження та відхилення на поверхнях деталі, що не виглядають. Наповнення, усадка та викид цвілі також повинні впливати на рішення щодо розміщення ребер.
Ребра, які не стикуються з вертикальною стінкою, не повинні різко закінчуватися. Поступовий перехід до номінальної стінки повинен зменшити ризик концентрації стресу.
Ребро - розміри
Ребра повинні мати такі розміри.
Товщина ребра повинна становити від 0,5 до 0,6 номінальної товщини стінки, щоб уникнути слідів раковини.
Висота ребра повинна бути в 2,5-3 рази номінальна товщина стінки.
Ребро повинно мати кут тяги від 0,5 до 1,5 градуса для полегшення виштовхування.
Основа ребра повинна мати радіус від 0,25 до 0,4 номінальної товщини стінки.
Відстань між двома ребрами повинна становити від 2 до 3 (або більше) номінальної товщини стінки.
8. опрацьовані краї
Коли дві поверхні стикаються, це утворює кут. На куті товщина стінки збільшується в 1,4 рази від номінальної товщини стінки. Це призводить до диференціальної усадки та формованого напруження та довшого часу охолодження. Отже, ризик відмови в обслуговуванні зростає за різких кутів.
Щоб вирішити цю проблему, кути слід згладити радіусом. Радіус повинен забезпечуватися як зовні, так і всередині. Ніколи не майте внутрішнього гострого кута, оскільки він сприяє появі тріщин. Радіус повинен бути таким, щоб вони підтверджували правило постійної товщини стінки. Бажано мати радіус від 0,6 до 0,75 разів товщини стінки по кутах. Ніколи не майте внутрішнього гострого кута, оскільки він сприяє появі тріщин.
9. гвинт дизайн боса
Ми завжди використовуємо гвинти, щоб закріпити дві напівкружки разом, або закріпити PCBA або інші компоненти на пластикових деталях. Отже, гвинтові головки - це конструкція для вкручування та закріплення деталей.
Головка гвинта має циліндричну форму. Бос може бути пов'язаний в основі з материнською частиною або може бути пов'язаний збоку. З’єднання збоку може призвести до утворення товстого пластику, що є небажаним, оскільки може спричинити появу слідів раковини та збільшити час охолодження. Цю проблему можна вирішити, прив’язавши головку крізь ребро до бічної стінки, як показано на ескізі. Бос можна зробити жорстким, забезпечивши контрфорсні ребра.
Гвинт використовується на головці для кріплення якоїсь іншої частини. Існують гвинти, що утворюють різьблення, і гвинти з різанням протектора. Гвинти для формування різьби застосовуються на термопластах, а гвинти для різання різьби - на нееластичних термореактивних пластикових деталях.
Гвинти, що формують різьбу, створюють внутрішні нитки на внутрішній стінці боса холодним потоком - пластик деформується локально, а не ріжеться.
Головка гвинта повинна мати належні розміри, щоб витримувати зусилля вставки гвинта та навантаження, що покладається на гвинт, що працює.
Розмір отвору щодо гвинта є критичним для стійкості до зачищення різьби та витягування гвинта.
Зовнішній діаметр головки повинен бути достатньо великим, щоб витримувати напруги обручів через формування різьби.
Діаметр отвору має трохи більший діаметр у в'їзді на невелику довжину. Це допомагає знаходити гвинт перед забиванням. Це також зменшує напруження на відкритому кінці головки.
Виробники полімерів дають рекомендації щодо визначення розміру поглиблення для своїх матеріалів. Виробники гвинтів також дають рекомендації щодо правильного розміру отвору для гвинта.
Слід подбати про те, щоб забезпечити міцні зварні з'єднання навколо гвинтового отвору в патроні.
Слід бути обережним, щоб уникнути напруги в начальника, оскільки він може зазнати невдачі в агресивному середовищі.
Отвір у босі повинен бути глибшим, ніж глибина різьби.
10.Оздоблення поверхні
Іноді, щоб отримати гарний зовнішній вигляд, ми часто робимо спеціальну обробку на поверхні пластикового корпусу.
Такі як: текстура, високоглянцевий, фарбування спреєм, лазерне гравірування, гаряче тиснення, гальванічне покриття тощо. Необхідно враховувати при проектуванні виробу заздалегідь, щоб уникнути подальшої обробки не може бути досягнуто або зміни розміру, що впливають на складання виробу.